4140 steel – an all-rounder with excellent performance
4140 steel and it’s equivalent steel chemical composition :
Grade | C | Si | Mn | S | P | Cr | Mo | Ni | V | W |
4140 | 0.38-0.43 | 0.15-0.35 | 0.75-1.00 | ≤0.040 | ≤0.035 | 0.80-1.10 | 0.15-0.25 | / | / | / |
EN19 | 0.36-0.44 | 0.10-0.40 | 0.70-1.00 | ≤0.040 | ≤0.035 | 0.90-1.20 | 0.15-0.25 | / | / | / |
42CRMo | 0.38-0.45 | 0.17-0.37 | 0.50-0.80 | ≤0.035 | ≤0.035 | 0.90-1.20 | 0.15-0.25 | / | / | / |
42CRMo4 | 0.38-0.45 | ≤0.40 | 0.60-0.90 | ≤0.035 | ≤0.025 | 0.90-1.20 | 0.15-0.30 | / | / | / |
SCM440 | 0.38-0.43 | 0.15-0.35 | 0.60-0.85 | ≤0.030 | ≤0.030 | 0.90-1.20 | 0.15-0.30 | / | / | / |
The exquisite combination of these elements gives 4140 steel the perfect blend of high strength and toughness.
After quenching and tempering, it exhibits excellent comprehensive mechanical properties,
- Tensile Strength: Typically Min 1080 MPa
- Yield Strength: Min 930 MPa
- Area Reduction: Min 45%
- Impact energy :Min 63J
- Impact toughness value: Min 78J/cm²
- Hardness: 28-32HRC
Not only that, the addition of molybdenum and chromium significantly improves its wear resistance and fatigue resistance, allowing it to maintain stable performance under repeated stress conditions. At the same time, 4140 steel also has excellent machinability, easy cutting and forming, and good heat treatment responsiveness. It can accurately adjust the hardness and toughness through different heat treatment processes, such as normalizing, quenching + tempering(QT), to suit diverse applications. Application requirements have also enabled it to show its talents in many fields such as aerospace, automobiles, and machinery manufacturing.
The “steel backbone” of the aviation field
(1) Solid support of the landing gear
In the aerospace industry, 4140 steel is the unsung hero. As a key component for takeoff and landing, aircraft landing gear must withstand huge impact forces and heavy loads. After proper heat treatment, 4140 steel has a tensile strength of over 1500MPa and a yield strength of over 1300MPa, making it easy to handle. Like the Boeing 737 series aircraft, some key parts of the landing gear are made of 4140 steel. The impact force at the moment of landing can reach hundreds of tons. With its high strength, good toughness and hardenability, it ensures the structural integrity of the landing gear and allows the aircraft to touch the ground smoothly. Glide safely.
(2) Responsible for the stability of the fuselage structure
The fuselage structure is also inseparable from 4140 steel. When flying in the air, the fuselage is subjected to complex stresses, including air pressure differences, torque from maneuvering flight, etc. 4140 steel is used in key parts such as fuselage beams and frames. It has excellent fatigue resistance and can withstand millions of stress cycles without crack initiation. At the same time, compared with some high-strength but high-density steels, it has a suitable strength-to-weight ratio, which can reduce weight while ensuring the stability of the fuselage, improve fuel efficiency, help the aircraft have longer range and better economy, and provide benefits to the aviation industry. Development has made great contributions.
“Right-hand assistant” in the field of automation
(1) The first choice for precision mechanical parts
In the field of automated production, 4140 steel is also a “powerful candidate”. It is the best choice for manufacturing precision mechanical parts, such as high-precision gears, shafts, etc. Its good machinability allows it to easily achieve micron-level processing accuracy during turning, milling, grinding and other processing processes, meeting the stringent requirements of automation equipment for precision fit of parts. Moreover, through proper heat treatment, the hardness can be controlled in the HRC 30-40 range, which not only ensures high strength but also takes into account toughness, allowing parts to stably transmit power under high-speed operation and frequent starts and stops, and reduce the risk of wear and fatigue failure. , greatly improving the operational reliability and lifespan of automated production lines.
(2) Reliable guarantee of industrial automation equipment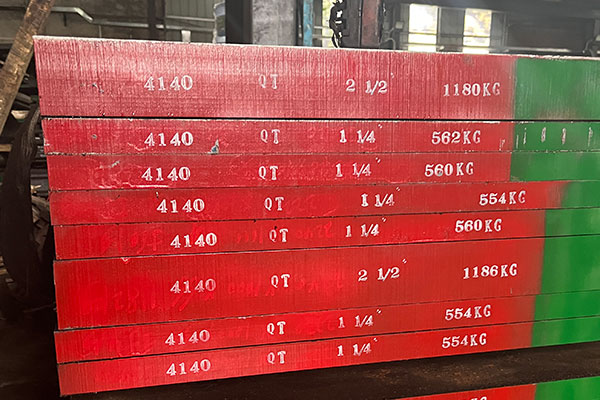
4140 steel is often found in key parts such as frames and guide rails of industrial automation equipment. When the equipment is running, the frame must bear the weight of many components and resist vibrations, and the guide rails must ensure that the slider moves smoothly and accurately. With its excellent wear resistance, 4140 steel can still maintain dimensional accuracy after long-term use, reducing the risk of equipment accuracy drift; its excellent anti-fatigue performance can withstand millions of stress cycles, eliminate cracks, and ensure the stability of equipment for many years. operation, greatly reducing the company’s downtime maintenance costs caused by equipment failure, and laying a solid foundation for the efficient advancement of automated production.
Professional steel supply and quality assurance
As a professional supplier specializing in 4140 steel, we feel a heavy responsibility. In terms of quality control, from the strict screening of raw material procurement, to the precise control of every step of the production process, to the comprehensive inspection of finished products before leaving the factory, we ensure that every batch of 4140 steel meets or even exceeds industry standards. Whether it is tensile strength, yield strength, hardness, toughness and other key indicators, there are detailed data to support the quality.
In terms of inventory, we always have a wide range of 4140 steel in stock, covering round bars of different diameters, plates of various thicknesses, and profiles of various sizes to meet the diverse needs of customers. Whether you are in small batch trial production or large-scale production, we can quickly Respond to supply.
Not only that, we also provide customized services, tailor-made exclusive material solutions based on customers’ special composition fine-tuning and heat treatment requirements for steel; our after-sales team is on standby to answer your questions during use and solve technical problems, making your purchase smooth. worry. Choosing us means choosing professionalism, reliability and peace of mind, and working together to create a brilliant future.