Will stainless steel rust? At first glance, it seems to be a false proposition. But stainless steel rust is everywhere in life, such as the picture below!
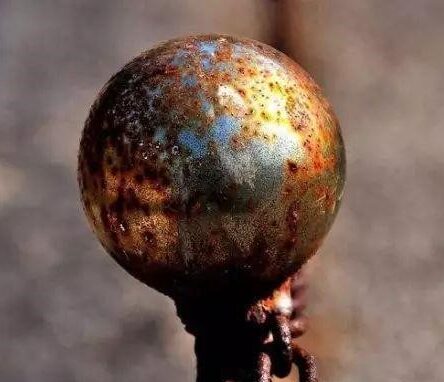
Why does iron rust?
When iron is exposed to the air, it reacts chemically with oxygen and moisture to produce various iron oxides, which is manifested as “rust”!
What is stainless steel?
Different from normal steels , stainless steel is a type of steel that has the ability to resist atmospheric oxidation and also has the ability to resist corrosion in media containing acids, alkalis, and salts!
Introduction to stainless steel
In layman’s terms, stainless steel is steel that does not rust easily. In fact, some stainless steel has both rust resistance and acid resistance (corrosion resistance). The rustlessness and corrosion resistance of stainless steel are due to the formation of a chromium-rich oxide film (passivation film) on its surface. This film isolates the metal from the external medium, prevents the metal from being further corroded, and has the ability to repair itself. , if once damaged, the chromium in the steel will regenerate a passivation film with the oxygen in the medium to continue to play a protective role.
The decisive factor in the stainlessness of stainless steel is the chromium content. It is reported that the standards of European and American countries stipulate that the minimum chromium content cannot be less than 10.5%, Japan’s stipulation is 11%, and China’s is 12%.
Stainless steel classification
There are five basic types of stainless steel: austenitic, ferritic, martensite, duplex stainless steel, and precipitation hardening stainless steel.
There are five basic types of stainless steel: austenitic, ferritic, martensite, duplex stainless steel, and precipitation hardening stainless steel.
(1) Austenitic stainless steel is non-magnetic. The typical steel type is added with 18% chromium and contains a certain amount of nickel to increase corrosion resistance. They are widely used steel types.
(2) Ferrite is magnetic and its main content is chromium, with a proportion of 17%. This material has good oxidation resistance.
(3) Martensitic stainless steel is also magnetic. The chromium content is usually 13% and contains an appropriate proportion of carbon.
(4) Duplex stainless steel has a mixed structure of ferrite and austenite. The chromium content is between 18% and 28%, and the nickel content is between 4.5% and 8%. They have great resistance to chloride corrosion. Good results.
(5) The conventional chromium content of precipitated stainless steel is 17, with a certain amount of nickel, copper and niobium added, which can be hardened through precipitation and aging.
According to the metallographic structure, it can be divided into:
- Ferritic stainless steel (400 series), which is chromium stainless steel, the main representatives are 420, 440, etc.;
- Austenitic stainless steel (300 series), chromium-nickel stainless steel, the main representatives are 304, 316, 321, etc.;
- Martensite Stainless steel (200 series), chromium-manganese stainless steel, high carbon content, the main representatives are 1Gr13, etc.
Why stainless steel resists rust
Elements such as nickel and nickel are added to the surface of stainless steel to form an extremely thin, strong, fine, and stable chromium-rich oxide film (protective film), which prevents oxygen atoms from continuing to penetrate and oxidize, thereby gaining the ability to resist rust.
Why does stainless steel also rust?
Stainless steel will rust when the dense oxide protective layer is destroyed.
Under what conditions will the protective film be damaged?
- Bleaching powder
- Mechanical wear
- Water
Application areas of stainless steel
There are many types of stainless steel, with different properties and different use environments.
301—Good ductility, used for molded products. It can also be hardened by mechanical processing with good weldability. Furthermore,wear resistance and fatigue strength are better than 304 stainless steel.
302—The corrosion resistance is the same as that of 304, but its strength is better due to its relatively higher carbon content. Often used in the food industry
316—Compare with 304, the 316 most widely used steel type, mainly used in the food industry and surgical equipment, the addition of molybdenum gives it a special structure that resists corrosion. Because it has better resistance to chloride corrosion than 304, it is also used as “marine steel”. SS316 is usually used in nuclear fuel recovery devices.
420—”Cutting grade” martensitic steel, similar to Brinell high chromium steel, the earliest stainless steel. Also used in surgical knives, which can be made very shiny.
430—ferritic stainless steel, for decorative purposes, such as automotive accessories. Good formability, but poor temperature resistance and corrosion resistance.
440—High-strength cutting tool steel with slightly higher carbon content. After appropriate heat treatment, it can obtain higher yield strength and its hardness can reach 58HRC, which is among the hardest stainless steels. The most common application example is “razor blades”. There are three commonly used models: 440A, 440B, 440C, and 440F (easy-to-process type).
In addition to 300 series and 400 series, there are also 500 series – heat-resistant chromium alloy steel, 600 series – martensitic precipitation hardening stainless steel
Stainless steel materials may rust due to the following reasons:
There are chloride ions in the use environment
Chloride ions exist widely, such as table salt/sweat stains/sea water/sea breeze/soil, etc. Stainless steel corrodes very quickly in the presence of chloride ions, even more than ordinary low carbon steel. Therefore, there are requirements for the environment in which stainless steel is used, and it needs to be wiped frequently to remove dust and keep it clean and dry. (This would give him an “inappropriate use” rating.)
Without solid solution treatment
The alloy elements are not dissolved into the matrix, resulting in a low alloy content in the matrix structure and poor corrosion resistance.
Natural intergranular corrosion
This titanium- and niobium-free material is prone to intergranular corrosion.
The most common ways to destroy the passive film of stainless steel in daily life are as follows:
1. Dust containing other metal elements or attachments of heterogeneous metal particles accumulate on the surface of stainless steel. In humid air, the condensed water between the attachments and stainless steel connects the two into a micro-battery, triggering an electrochemical reaction. , the protective film is damaged, which is called electrochemical corrosion.
2. Organic juice (such as vegetables, noodle soup, etc.) adheres to the surface of stainless steel. In the presence of water and oxygen, it forms organic acid. For a long time, the organic acid corrodes the metal surface.
3. The surface of stainless steel contains acid, alkali, and salt substances (such as alkaline water and lime water splash on the wall decoration), causing local corrosion.
4. In polluted air (such as an atmosphere containing a large amount of sulfides, carbon oxides, and nitrogen oxides), when encountering condensed water, sulfuric acid, nitric acid, and acetic acid liquid points will form, causing chemical corrosion.
To ensure that metal surfaces are permanently bright and free from rust, here are some suggestions:
1. The surface of decorative stainless steel must be cleaned and scrubbed frequently to remove attachments and eliminate external factors that cause modification.
2. 316 stainless steel should be used in seaside areas. 316 material can resist seawater corrosion.
3. The chemical composition of some stainless steel pipes on the market cannot meet the corresponding national standards and cannot meet the 304 material requirements. Therefore, it will also cause rust, which requires users to carefully choose products from reputable manufacturers.
So stainless steel is not that it will not rust, but it is not easy to rust!
If you want to know more information about stainless steel ,please do not hesitate contact us.